Balloffet designs and realizes the best drawing dies, single or polycrystalline diamond, natural or synthetic.
We advise you to obtain the dies adapted to the metal or drawn alloy.
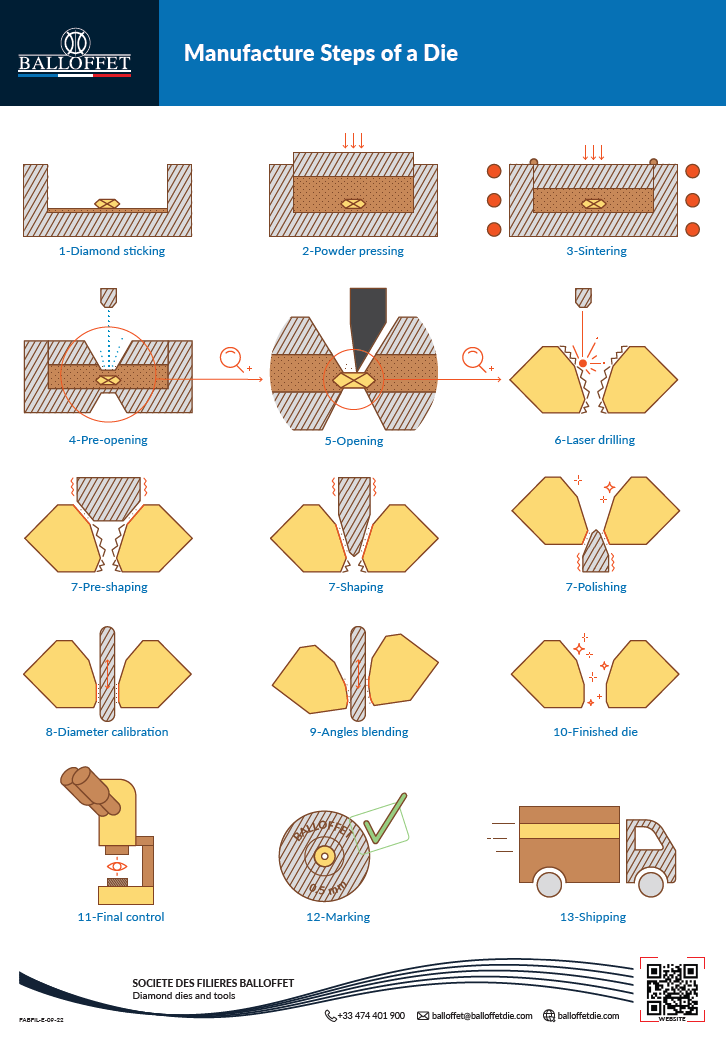
Die internal Geometry
A wire drawing die is first used to stretch a wire to reduce it to the desired diameter. Whatever its use, the inner geometry of the die is always broken down into 5 parts, each of which plays an essential role in the drawing process: entry cone, reduction cone, bearing, back-relief, exit cone.
These 5 parts feature the internal geometry of the die which will be determined according to the characteristics of the material to be drawn and the drawing conditions (lubrication type, speed, elongation, etc.)
This geometry also has a great influence on the properties of the drawn body (wire, bar, tube, etc…): cold working, ductility, straightness, surface condition, etc.
Finally, the die is a tool whose study in the microscope after drawing, gives many indications on the conditions of use and on the possible improvements to be made (lubrication, filtration, etc…).

Key elements determining a high-performance die

The diamond drawing dies must combine performance, longevity and competitiveness. Several elements make the difference:
- Raw materials Quality
- Mounting Quality du montage (mechanical and thermal)
- Accuracy and regularity of the inner geometries
- Final polishing
The quality of the raw materials is crucial, the process and the technologies used are decisive and the human know-how remains decisive!